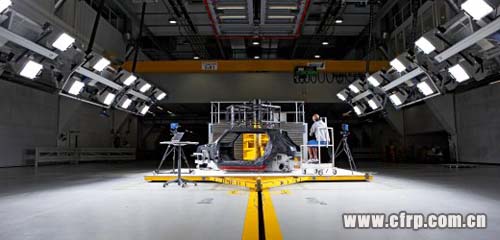
据日经BP社报道,CFRP(碳纤维增强树脂基复合材料,简称碳纤维复合材料)与钢板及铝合金相比,虽可大幅减轻重量,但因为成本高,此前只被用在赛车及超级车上。目前业内正在开发可快速且低成本制造CFRP的技术。在已有使用先例的热塑性CFRP方面,出现了采用RTM(树脂传递模塑)成型工艺使成型品的成本降至以往的1/5~1/7的“可行方案”。而且,为了能够在2020年前后正式采用,业内也开始挑战利用热塑性CFRP将成本降至1/10以下的“理想方案”。
RTM工艺可使高强度高刚性的热塑性CFRP快速成型。通过成型后再向模具中注入树脂,以及在强化纤维中不使用纺织品的改进措施来降低成本。采用该工艺每月可生产数千个CFRP部件,成型品的成本也有望降至原来的1/5~1/7。宝马公司的“i3”与丰田的“雷克萨斯LFA”均积极导入了RTM工艺。另外,使用原来的预浸料也可在5~10分钟内成型的技术也已诞生。 copyright 123456
在赛车及跑车中使用最多的是将预浸料层叠并利用热压使其固化的热塑性CFRP。比如,日产汽车的“LEAF”(中国名:聆风)的马达、再比如将减速机中置的EV赛车“LEAF NISMO RC”演示款都使用预浸料制造了从驾驶室到通风罩的绝大部分部件(图1)。
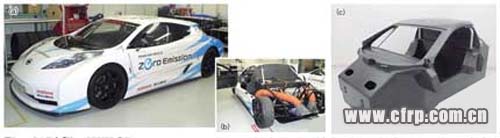
图1 日产汽车的“LEAFNISMO RC”
(a)驾驶室与通风罩使用了CFRP,重量为925kg,比量产车轻了495kg。(b)马达中置。(c)单体车身以预浸料工艺成型,上部以防滚架加固。驾驶座后方装有锂离子充电电池。
制造上述车辆的NISMO(日产赛车运动国际公司)还采用相同的方法制造了参加全日本GT锦标赛“GT500”级别比赛的“GTR”的CFRP驾驶室。LEAF NISMO RC尽可能地去掉了GT车使用的夹在预浸料之间的蜂窝面板及嵌入部件,通过简化构造,降低了驾驶室的制造成本。
copyright 123456
虽说成本大幅低于GT车,但LEAF NISMO RC的驾驶室的制造成本仍高达数百万日元,这个价格可以买一辆汽车了。单壳体车身的重量为150kg,单位重量的成本非常高,折合每公斤数万日元。
不使用热压罐
原来的制造方法因层叠预浸料需要花费人力,而且使用热压罐的固化时间较长,所以成本较高。因此,研究人员为降低成本而省去了层叠工序及热压罐固化工序,改进了成型工艺。
改进的成形工艺主要有两种,一种是为成型飞机部件等不需要入炉的大型部件而开发的VaRTM(真空辅助树脂传递模塑),另一种就是RTM(图2)。VaRTM是在模具内层叠碳纤维,以薄膜袋包覆模具后进行真空处理,这一点与预浸料的成型相似。但该方法不使用热压罐,而是利用真空负压使树脂浸渍在纤维中,然后对模具加热使其固化。
本文来自123

图2 VaRTM(Vacume assisted RTM)与RTM(丰田的比较)
RTM工艺以上下模具夹住预成型坯(将纤维片层叠后按最终形状赋形并临时焊接),然后向模具内注入树脂并使其固化。
富士重工业2011年发售的400辆限量车型“翼豹WRX STItS”的车顶就使用了VaRTM工艺〔图3(a)〕。据该公司介绍,在小批量生产时,因不需要制造模具,所以模具费用低于RTM。

图3 富士重工业的“翼豹WRX STI tS”的车顶
(a)采用东丽的VaRTM工艺成型,车顶的重量减轻到了5kg。(b)前后夹住树脂垫圈以螺钉固定,左右螺母部分进行了阳离子电沉积涂装
翼豹WRX STItS的车顶重叠了4层将纤维织成格子状的“平织”片材并注入了树脂。对模具加热30分钟左右使其固化后,再进行热处理后工序,最后进行涂装。该部件由东丽负责成型,碳纤维使用了名为“T300”的拉伸强度达到3.5GPa的通用产品,纤维为将3000根纤维丝扎成一束的“3k”产品。
123456
车顶的刚性非常重要。碳纤维单体的弯曲刚性较高,但CFRP由于改变了纤维的方向并将其层叠在一起,所地会导致某个方向的刚性降低。为此,相对于铁(Fe)制车顶的厚度为0.7mm,CFRP车顶的厚度却达到了1.6mm,为前者的两倍以上,由此来确保刚性。而质量则由10kg减至6kg(车顶本身为5kg),减轻了4kg。
车顶以粘合方式及螺钉来固定在车身上,前后和左右均有8个螺钉固定。改进点是,为了防止Fe与CFRP的接触部发生电解腐蚀,采取了用聚氨酯垫圈来绝缘、使用不锈钢螺钉、以及对嵌入件施以阳离子电沉积涂装等措施〔图3(b)〕。
量产性较高的RTM工艺
采用VaRTM工艺虽可在小批量生产时减少模具费用,但成型时间长达4个小时。作为维修部件单独购买翼豹的车顶时,价格高达35万日元。即便按成本为售价的一半来计算,成型品单位重量的成本也达到了3.5万日元/kg,与采用预浸料的方法差别不大。
123,123
RTM很有希望成为进一步降低成本的方法。RTM工艺需要上下模具及树脂注入机,虽然初始投资较高,但成型时间只有7~90分钟。由于能够缩短成型时间,因此可大幅降低每个部件的设备折旧费。
除了迈凯轮的MP4-12C及意大利兰博基尼的“AventadorLP 700-4”在驾驶室成型时采用了RTM工艺之外,年产1万辆以上的宝马“i3”也采用了该工艺。
下面以i3为例推算一下RTM成型品的成本。假设车辆价格为400万日元,车身价格应该低于100万日元,在此暂且假设车身成本为50万日元。该车的EV模式续航距离可达到130~160km,因此需要容量为20kWh左右的锂离子充电电池,光是电池成本就需要100万日元以上,所以能划分给车身的成本肯定不多。假设驾驶室的重量为Fe车身200kg左右的一半,也就是100kg,驾驶室成本为50万日元的话,成型品成本就是5000日元/kg。
copyright 123456
该车之所以大胆采用CFRP驾驶室,是因为轻量化车身有利于减少搭载的锂离子充电电池的容量,从而削减电池部分的成本。i3在兼做电池保护架的铝合金梯形车架上,安装了CFRP驾驶室,以螺钉和粘合方式将二者固定在一起(图4)。如果车身较轻,便可相应地减少电池的容量。

图4 宝马“i3”的试制车身
在装有锂离子充电电池与悬挂的铝合金底盘上,安装了CFRP车身。
通过多轴基材降低材料成本
为降低材料成本,技术人员改进了从预成型坯使用的片材、纤维到原料的整个供应链。RTM成型的绝大部分部位都采用多轴基材,该材料是将纤维单向排列、用白线缝合而成的。
多轴基材将UD(单向)片材以相互垂直的方向层叠起来,然后将其缝合在一起,使之同时具备X轴及Y轴方向的强度。CFRP大多使用“平织”片材,但不需要编织的UD材料造价较低(图5)。
123456
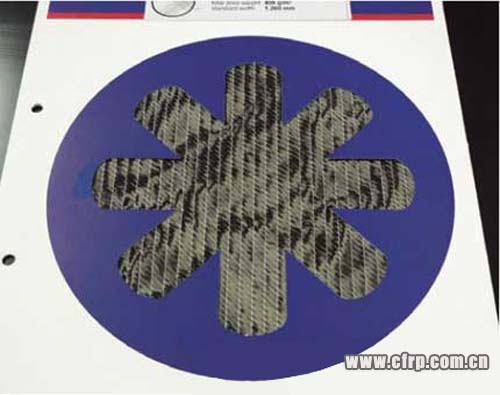
图5 德国西格里集团的多轴基材
重叠了方向互相垂直的纤维,通过缝合实现了一体化。该公司也向宝马公司供应这样的材料。
技术人员还改进了纤维丝的制造工艺。为宝马公司供应的碳纤维以PAN(聚丙烯)纤维为原料,该原料由三菱丽阳与德国西格里集团的合资公司制造。PAN纤维在宝马与西格里集团的合资工厂灼烧后制成碳纤维,通过预先扎成较粗的“5k”(5000根)束,实现了UD片材的低成本制造。
在RTM工艺中使用中空预成型坯
使用多轴基材的RTM实例是,以前就开始采用CFRP的宝马“M3”车顶成型工艺。首先,将轧辊放在预成型坯成型机上拉出纤维〔图6(a)〕。然后将纤维放在预成型坯的成型模具上〔图6(b)〕。此时,为了临时粘合层叠起来的各层片材,需要预先涂上粘合材料。接下来,关闭模具进行加热,使预成型坯凝固成车顶的形状,然后冲切掉溢出模具的部分〔图6(c)〕。再用机器人将预成型坯投入RTM成型机,注入树脂使其固化〔图6(d)〕。
内容来自123456
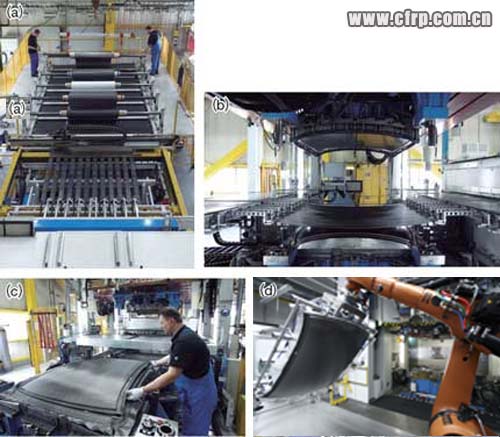
图6 RTM的成型工序
(a)从轧辊上拉出碳纤维,(b)将纤维放在对预成型坯成型的模具上,(c)涂上粘合剂后关闭模具,让预成型坯凝固并切边,(d)机器人将预成型坯投入RTM成型机。
虽然i3的侧板是作为具有大尺寸开口部的单张板成型的,但预成型坯被分成了几个小块。制作侧板的成型品(图7)时,用装订机将成型坯的重叠部分固定在一起,将预成型坯的小块连在一起,作为大预成型坯放在模具中。而后挡泥板等则由多个部件成型后粘合而成。
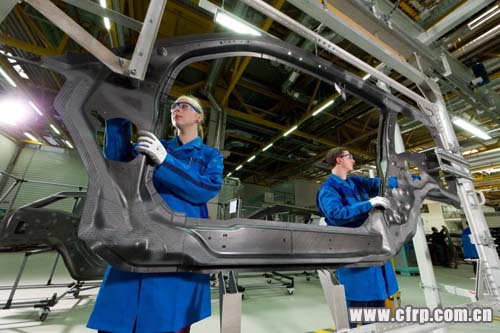
图7 i3的侧板
分成小部件来制作预成型坯,用装订机固定重叠部分。采用RTM成型工艺制成一体化的侧板。
除了多轴基材以外,i3的CFRP部件还采用了中空形状的预成型坯,例如车窗周围就使用了像绳扣一样编织的预成型坯(图8,图上看不到)。该部分采用了利用发辫原理制造绳索或带子的编织技术。形成中空形状时,将纤维编织缠绕在用失蜡铸模制造的芯轴上,RTM成型后再将芯轴熔化掉。
内容来自123456

图8 车窗周围使用了编织物预成型坯
图片中看不出来,车窗周围的车顶及发动机罩附近的水平部材使用了像绳扣一样的编织物。
该技术还被用在了宝马上一代“M6”的前后保险杠上(图9)。预成型坯的成型由西格里集团旗下的德国SGL Kumpers公司负责,编织机由德国August Herzog生产。
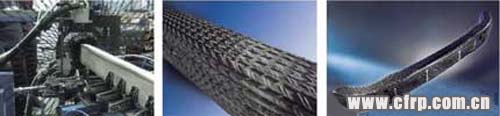
图9 上一代“M6”的保险杠也使用了编织物预成型坯
由SGL Kumpers负责成型。左起分别为August Herzog公司的编织机、编织物预成型坯、RTM成型品。
LFA在3处采用了RTM工艺
日本厂商方面,丰田的雷克萨斯LFA是首款CFRP车。该车最初采用铝(Al)合金设计,但中途改成了CFRP设计,驾驶室由CFRP制成,底盘部分由铝合金制成。白车身重量为193kg,比使用铝合金时减轻了约100kg(图10)。
123,123
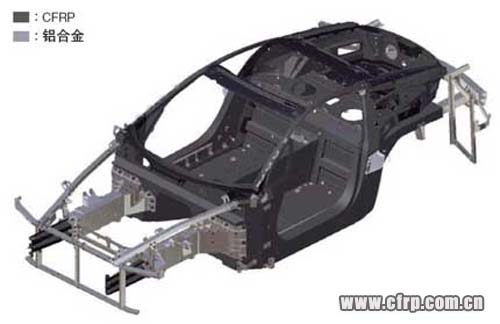
图10 丰田“雷克萨斯LFA”的白车身
重量为193kg,其中CFRP占65%,铝合金占35%。
制造雷克萨斯LFA驾驶室时采用了三种成型方法。侧栏及前部舱壁等具有中空构造的主要骨架采用了预浸料工艺,前部碰撞吸能盒、A柱及地板采用了RTM工艺,后部部件采用了以碳纤维加固的SMC(片状模压料)成型工艺(图11)。
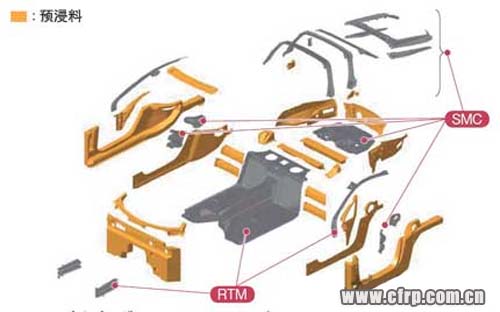
图11 采用预浸料、RTM及SMC工艺
大部分采用预浸料工艺,地板、A柱及碰撞吸能盒采用RTM工艺制成。后部部件采用SMC成型工艺制成。
驾驶室是在采用各种方法成型的部件上涂粘合剂,放在夹具上,在炉内固化60分钟使其合为一体。外板方面,采用RTM工艺制成了前部发动机罩,采用VaRTM工艺制成了CFRP车顶。
内容来自123456
主要骨架采用预浸料工艺的原因是小批量生产,而且由于是一次构造材料所以要具备充分的强度。此次,预浸料纤维使用了除气特性出色且能够提高强度的多轴基材。而且,并未使树脂完全浸渍在纤维束中,而是采用了处于半浸渍状态的“半浸料”,该材料基本不需要使用热压罐便可获得较高的质量。
RTM工艺由丰田自动织机协助开发,特点是将名为Vf的碳纤维含有率(质量百分比)提高到了55%左右,接近于预浸料的比率60%。设计之初,地板由6个部件粘合而成,因此需要很多模具。此次采用RTM工艺实现了一体成型,从而减少了部件数量和模具数量。
地板部分有10个预成型坯(图12)。各预成型坯利用专用模具按部品形状进行局部装配及预成型。将这些预成型坯、用于吸收侧面碰撞冲击能量的波板状部件,以及放入波板中空部的发泡芯放入模具,然后用RTM成型机注入环氧树脂和固化剂。成型时间为45分钟左右。
123456
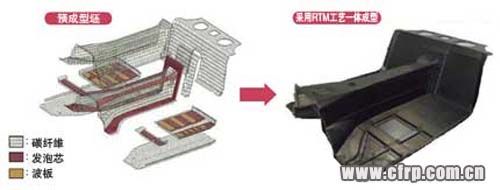
图12 地板采用RTM工艺将10个预成型坯合为一体
最初的设计将地板分为6个部件,后来采用RTM工艺统合成了一个部件。不仅减少了模具,还将工时缩短了80%,与粘合组装相关的机械加工减少了50%。成型时结合使用了RTM工艺与注入压缩工艺。
预成型坯使用了多轴基材(图13)。丰田有机材料技术部长、负责雷克萨斯LFA开发的小泽学表示:“多轴基材的特点是成本较低,与织物不同,纤维呈直线状,所以可提高强度”。
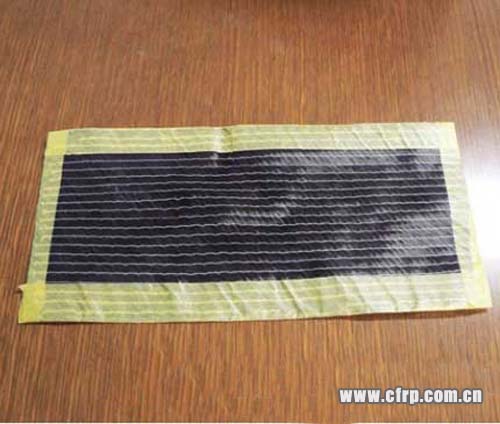
图13 RTM用多轴基材
与宝马的基材一样,重叠并缝合了两张方向相互垂直的纤维。
A柱预成型坯使用的中空编织物是利用村田机械的编织机生产的。该编织机不仅可改变编织物的截面形状,还能使芯轴往返,通过重叠数层来增加编织物的厚度。LFA的A柱最厚部分使芯轴往返了6次,重叠了12层。如图14所示,A柱与平板状支架采用RTM工艺一体成型。而且,平板使用了外板剩余的边角料,有效利用了昂贵的碳纤维。
copyright 123456
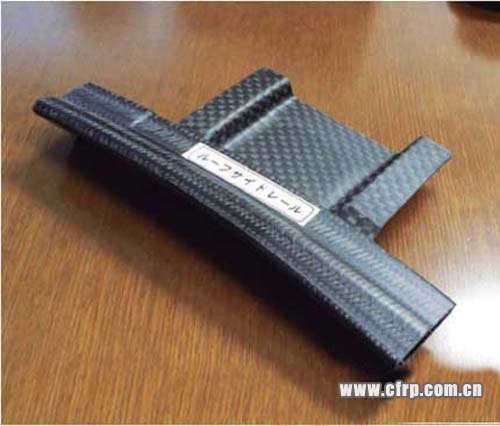
图14 用编织物制作预成型坯的A柱
以编织物制作了中空形状的预成型坯。采用RTM工艺将其与利用边角料的支架一体成型。
此外,丰田自动织机公司还开发出了三维织物(图15),可用于碰撞吸能盒的新预成型坯。该产品并不是二维纤维片,在将纤维片层叠之后还沿着Z轴方向穿过了纤维丝(图16)。
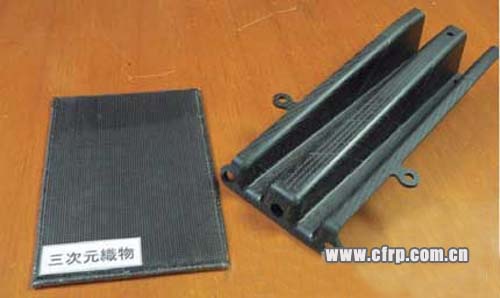
图15 三维织物与碰撞吸能盒
碰撞吸能盒的前端截面积较小,往后逐步增大,使其在碰撞时从前端开始变形。
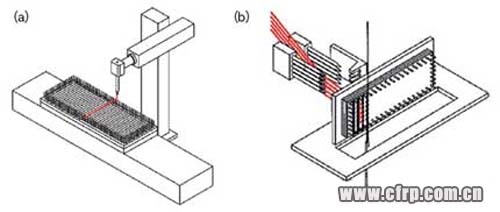
图16 三维织物的织机
(a)由缠绕在四周竖起的纺针上制造纤维片的装置,以及(b)沿着厚度方向插入纤维丝的装置构成。可制造厚度为10mm以上的织物。
内容来自123456
CFRP碰撞吸能盒的特点是冲击能量吸收功能出色,其比强度大于金属,而且不像金属制品那样会留下压碎的残留物。据东丽介绍,CFRP吸能盒单位重量吸收的能量比铁制品高2.5倍。丰田自动织机此次开发的织物在遭到破坏时碳纤维夹层不会剥离,吸收能量是二维产品的1.2~1.5倍。
东丽实现RTM高速化
东丽为了降低成型成本,在RTM工艺的高速成型方面作出了不懈努力。以LFA为例,本来成型时间为45分钟,东丽将其缩短到了7分钟,最终目标是5分钟。如果通过提高速度来降低成型成本,便有望将单位重量的成本降至原来的1/5~1/7。
东丽与英国Gordon Murray Design公司合作,制造出了CFRP概念车“TEEWAVE AR1”(图17),采用RTM工艺制造了驾驶室。驾驶室仅由3个部件构成,重量为45kg,比铁制驾驶室减轻了53%,但仍确保了12,000Nm/°的扭曲刚性,这一数值与普通车相当。
123,123
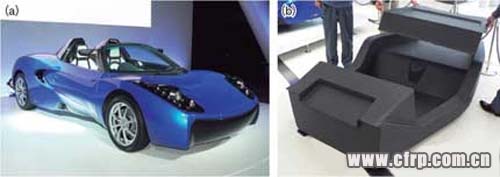
图17 东丽的CFRP试制车“TEEWAVE AR1”
(a)车身尺寸为长3975×宽1766×高1154mm,车身重量为846kg。其中锂离子充电电池重220kg。(b)驾驶室由三个RTM部件(地板、仪表板、后部面板)构成,重量为45kg。
东丽长期致力于RTM的高速成型,以前实现10分钟的成型时间时,预成型坯配置为1分钟,树脂注入为3分钟,树脂固化为5分钟,脱模为1分钟。为了将耗时最多的固化缩短至5分钟,该公司改进了固化剂。没有使用原来的胺类固化剂,而是开发出了注入之初缓慢凝固、随着不断固化而呈指数函数聚合的阴离子聚合类固化剂。
以上介绍的是生产效率高于预浸料工艺的RTM工艺应用范围不断扩大的情况,而三菱丽阳则采用了与其他公司不同的方法。该公司开发出了通过改进传统预浸料实现高速成型的技术“PCM(Prepreg Compression Molding)”。这是一种对预浸料进行热冲压成型的技术,成型时间只有5~10分钟,估计可实现与RTM工艺同等的成本。目前已开始向汽车厂商提供样品,最早将在两年左右以后实用化。
123456
PCM技术首先加热预浸料,并进行接近最终形状的预成型。然后,再将其投入正式模具中,进行热冲压成型。改进点是开发出了固化时间较短的树脂。
三菱丽阳试制的行李舱盖采用PCM技术制成了外侧,以预浸料热压罐成型技术制成了内侧,重量比相同形状的铝合金行李舱盖轻40%(图18)。厚度仅为1.1mm,重叠了5层UD预浸料。能够大幅实现薄型化的原因是,UD的强度比织物出色,而且优化了纤维的层叠方向。
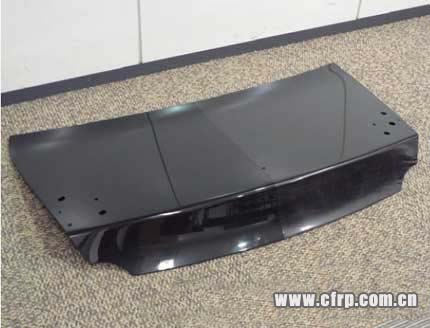
图18 三菱丽阳的热冲压成型品
对热塑性UD预浸料进行预成型之后进行热冲压。重量为2.4kg,比铝合金行李舱盖轻40%。内侧骨架以热压罐成型并粘合在一起。
据三菱丽阳介绍,PCM工艺的成型压力为3~10MPa,高于RTM的0.5~5MPa,成型品表面的平滑性也高于RTM工艺,而且压力达到2MPa以上时,表面不容易产生空隙等,可减少涂装的前处理等。
copyright 123456
PCM工艺适合比较简单的形状,很难实现有凸条花纹或深冲压的形状。实现复杂形状时,三菱丽阳打算将其与采用碳纤维的SMC工艺相结合。该公司还在开发在模具内与SMC一体成型以及形成中空部的技术(图19)。
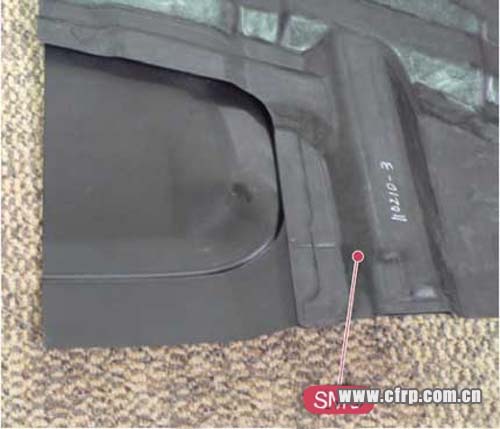
图19 内侧骨架采用SMC的实例
外侧采用预浸料工艺,内侧采用SMC工艺,在模具内同时成型为一体的前发动机罩。SMC工艺的形状自由度很高,适合复杂形状。
(日经BP社)